
BAE Systems has unveiled the digital techniques that are being used to design Britain’s Tempest sixth-generation fighter jet. By using a combination of computer-simulated digital twins and 3D-printed models, the goal is to simplify and speed up the development of the combat aircraft, which is scheduled to enter active service by 2035.
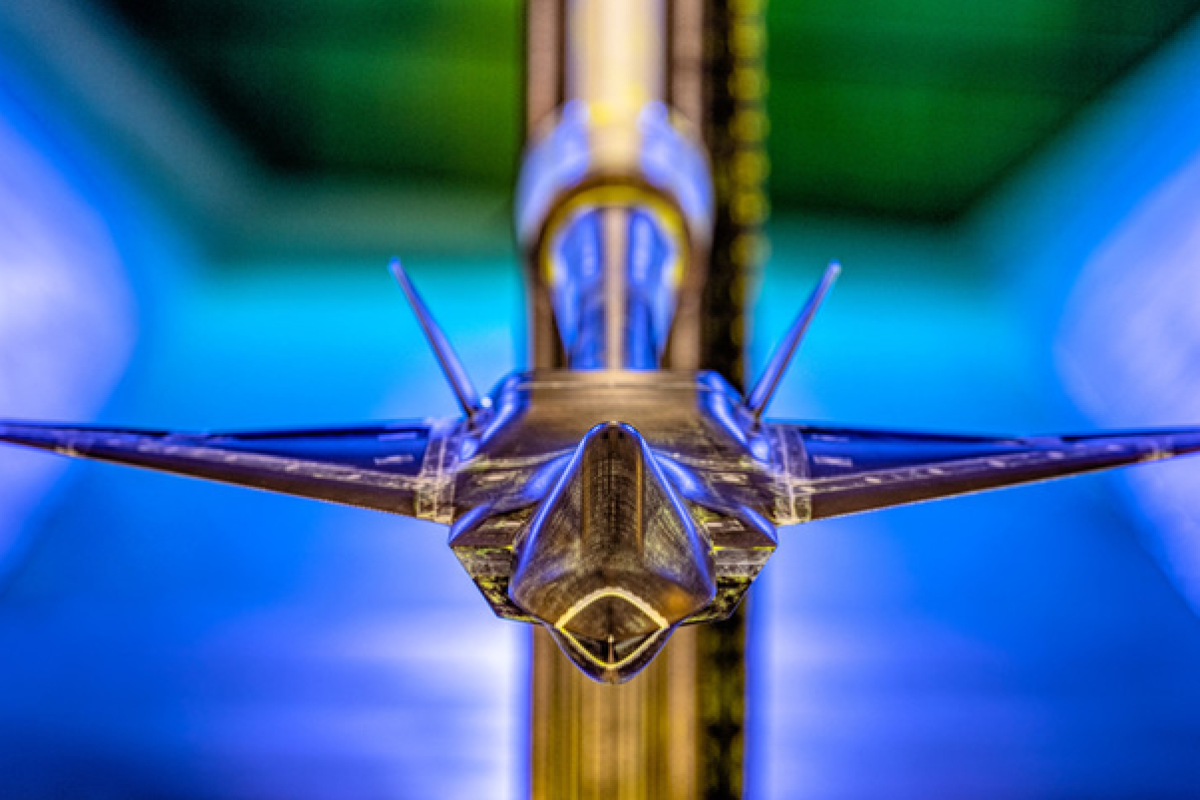
Still in the concept phase, the Tempest will be one of the first sixth-generation fighters and is designed to complement current combat craft like the F-35 Lightning II and the Typhoon fighters until they are retired in the 2040s. The twin-engine, delta-wing Tempest stealth fighter will be capable of carrying hypersonic missiles and controlling drone swarms.
It also has an advanced Rolls-Royce power and propulsion system that produces large amounts of electricity, allowing the fighter to power laser weapons.
In addition, it will have reconfigurable, artificial intelligence and cyber-hardened communications that allow the aircraft to act as a flying command and control center, with the pilot acting more as an executive officer than a dogfighter.
Inside, the Tempest will have a highly upgradable plug-and-play flexible payload system, a suite of integrated multi-spectral and radio-frequency sensors, and a virtual cockpit.
However, one of the big selling points of Tempest, which is a joint project by Britain, Sweden, and Italy, is the new digital system being developed by BAE to reduce the time from the drawing board to take off.
According to the company, Tempest is being virtually designed and tested using advanced computers to calculate the aerodynamic performance of different aircraft features. The system also allows test pilots to fly the Tempest’s digital twin in a ground-based simulator.
Though the digital twin is bleeding-edge technology, the aerodynamics of a fighter jet are so insanely complex that computer simulations quickly reach their limits. As a result, BAE is also creating 3D-printed models for supersonic wind tunnel tests to refine the shape of the aircraft.
“The digital twin concept we have developed will be used to design, test, and support every single system and structure for Tempest,” says Paul Wilde, Head of Airframe Technologies. “By taking an entirely digital approach to the challenge the UK Government has set us, we’re transforming the way we work and adding incredible value to the program. We can achieve what traditionally would have taken a number of months in a number of days. As a result, we’re working faster for the future, and we’re using the virtual environment to create endless opportunities for our engineers to experiment without boundaries, and with open minds – key to the future innovation of the program.”
BAE is also working with Rolls-Royce, Leonardo, and MBDA to advance technology in 60 areas, including advanced sensors and deep-learning artificial intelligence systems. The digital twin concept is also the basis for BAE’s Factory of the Future at Warton in Lancashire, which uses data from intelligent robots, supply chain databases, and machines to streamline the manufacturing of the Tempest, replacing traditional production lines with robotic ones that can rapidly adapt to design changes without the need for expensive and time-consuming retooling.
BAE and its partners will use the results of the current tests to produce an Outline Business Case for the British government as the next step in the Combat Air Acquisition Programme.
“Designing an aircraft has traditionally been an opportunity which comes up once in someone’s career which causes real challenges of transferring skills and knowledge,” says Michael Christie, Director, Future Combat Air Systems, BAE Systems.
“The technologies now available to us mean that we can reduce the design cycle which in itself is good for the affordability of a program, but we can also perform more cycles very quickly until we get it right. The UK Government has set us a significant challenge, but the program has some of the boldest and brightest minds on board, who are breaking milestones at an accelerated pace and developing technologies and techniques that will be game-changing for the UK defense industry and beyond.”
© 2020, GDC. © GDC and www.globaldefensecorp.com. Unauthorized use and/or duplication of this material without express and written permission from this site’s author and/or owner is strictly prohibited. Excerpts and links may be used, provided that full and clear credit is given to www.globaldefensecorp.com with appropriate and specific direction to the original content.
Be the first to comment